-
ООО ИТЦ «ДонЭнергоМаш»
-
Новокраматорский машиностроительный завод
-
НП инженеров «АВОК»
-
ООО «АйСиЭм Гласс Калуга»
-
Объединенный институт высоких температур РАН
-
ОАО «Таганрогский завод «Прибой»
-
ООО «Пластик Энтерпрайз»
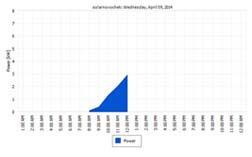
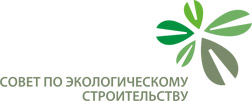
-
Отходы ТЭК. Общая характеристика
Общая характеристика отходов топливно-энергетического комплекса (ТЭК)
Существующие технологии производства и переработки угольной продукции объективно связаны с выходом большого количества твердых отходов. Техногенные месторождения в местах ликвидации угольных предприятий и твердые отходы при производстве угольной продукции занимают обширные площади земель, негативно воздействуют на состояние водных ресурсов, атмосферы. Предприятия угольной и топливно-энергетической отрасли расходуют значительные средства на транспортировку и складирование твердых отходов, платят за их размещение и загрязнение окружающей природной среды, возникающее вследствие вредных выбросов и сбросов в местах размещения терриконов и отвалов.
Золошлакоотвалы
Терриконы
К отходам топливно-энергетической промышленности относятся продукты, получаемые в виде отходов при добыче, обогащении и сжигании твердого топлива. Эту группу отходов разделяют по источнику образования, виду топлива, числу пластичности минеральной части отходов, содержанию горючей части, зерновому составу, химико-минералогическому составу, степени плавкости, интервалу размягчения, степени вспучиваемости.
Отходы добычи и обогащения угля. Основными видами твердого топлива являются каменные и бурые угли. При добыче и обогащении углей побочными продуктами служат шахтные и вскрышные породы, отходы углеобогащения.
Отходы добычи называют вскрышными или шахтными породами в зависимости от способа разработки. При подземном способе добычи извлекается меньше попутных пород, чем при открытом, но и они составляют значительные объемы. Так, например, на 1 т угля при открытой добыче образуется до 3-5 т вскрышных пород, при подземной – до 0,2-0,3 т шахтных.
Вскрышные и шахтные породы имеют неоднородный химический и минералогический состав и представляют осадочные породы – глины, суглинки, супеси, аргиллиты, песчаники, глинистые и песчаные сланцы, известняки. Больше всего в их составе аргиллитов (до 60%). Кроме того, они содержат в своем составе уголь до 20%, серу, содержание которой пропорционально содержанию угля, в небольших количествах цветные, редкие металлы.
Таблица – Гранулометрический состав отходов добычи угля (шахтных пород) Ростовской области
Класс размеров обломков, мм Содержание классов в объеме отвалов, % среднее пределы колебаний 0-6 12,8 2,0-70,0 6-50 23,9 3,0-60,0 50-70 22,1 2,0-50,0 70-100 21,3 3,0-50,0 100-450 14,5 0,0-76,0 более 450 5,4 0,0-32,0 Таблица – Химический состав отходов добычи угля (шахтных пород) Ростовской области
Содержание компонентов, мас. % п.п.п. SiO2 Al2O3 Fe2O3 CaO MgO SO3 TiO2 K2O Na2O MnO P2O5 S Cорг 3,19-21,11 45,1-62,0 14,89-21,5 1,89-7,72 0,68-6,6 1,05-2,69 0,05-4,27 0,71-1,27 3,05-4,89 0,85-1,46 0,01-0,11 0,14-0,37 0,12-1,86 1,22-8,57 Для применения в производстве строительных материалов наибольший интерес представляют отходы углеобогащения, характеризуемые наименьшими колебаниями состава и свойств. Содержание угля, не выделенного в процессе обогащения, может достигать 20%. Отходы углеобогащения представлены обычно в виде кусков крупностью 8-80 мм.
В соответствии с типовыми схемами технологического процесса обогащения уголь из шахт после измельчения подвергают гидравлической классификации по крупности, затем обогащают методом гравитации, выделяя концентрат, промышленный продукт и породу (отходы гравитационного обогащения углей). При обезвоживании концентрата выделяют шлам с размером зерен менее 1 мм, который направляют на флотацию. После флотационного обогащения получают концентрат и отходы флотации (хвосты).
В зависимости от способа получения отходов и их класса по крупности содержание угля, а соответственно химический состав и число пластичности изменяются в широких пределах. Наибольшее количество угля (15-40%) находится в отходах флотации. В отходах гравитационного обогащения класса 1-13 мм количество угля может достигать 15%, а в отходах класса 13-150 мм — 4-7%. В отходах угледобычи содержание угля колеблется от 0 до 10%. Весьма важным ограничивающим фактором применения отходов обогащения углей является наличие в них серы. Содержание ее, например, в породах центрального Донбасса достигает 3-4%.
Таблица – Химический состав отходов гравитационного обогащения углеобогатительных фабрик Ростовской области
Содержание компонентов, мас. % п.п.п. SiO2 Al2O3 Fe2O3 CaO MgO SO3 TiO2 K2O Na2O MnO P2O5 S Cорг 8,72-20,53 47,78-56,32 15,52-22,39 1,75-6,23 1,87-5,66 0,95-2,36 0,05-3,47 0,65-1,12 3,12-4,57 0,73-1,28 0,01-0,10 0,12-0,54 0,11-2,87 8,95-14,75 Таблица — Химический состав отходов флотации (шлам) углеобогатительных фабрик Ростовской области
Содержание компонентов, масс. % п.п.п. SiO2 Al2O3 Fe2O3 CaO MgO SO3 TiO2 K2O Na2O MnO Cорг 11,21-19,59 43,16-49,43 15,71-21,23 1,81-7,95 1,63-3,14 1,69-3,25 0,43-3,56 0,82-1,15 3,45-4,31 0,45-1,16 0,01-0,08 15,22-40,28 Влажность отходов зависит от способа их получения. Естественная влажность аргиллитов 4-5%. Отходы флотации углей, добываемые из шламонакопителей, имеют влажность 25-30%.
В отличие от отвальных пород угольных шахт отходы углеобогащения характеризуются более высоким содержанием угля, более стабильным вещественным составом, меньшим содержанием песчаников и большим содержанием аргиллитов, увеличением содержания серы и уменьшением механической прочности.
Продуктами обжига пустых пород, сопутствующих месторождениям каменных углей, являются горелые породы. Их разновидностями являются глиежи — глинистые и глинисто-песчаные породы, обожженные в недрах земли при подземных пожарах в угольных пластах, и отвальные перегоревшие шахтные породы.
Залежи природных горелых пород широко распространены в различных регионах. Истинная плотность их составляет 2,4-2,7 г/см³, средняя плотность — 1300-2500 кг/м³, прочность на сжатие — 20-60 МПа. По основным физическим и химическим свойствам они близки к глинам, обожженным при 800-1000 °С. Химико-минералогический состав горелых пород разнообразен, однако общим для них является наличие активного глинозема в виде радикалов дегидратированных глинистых минералов или в виде активных глинозема, кремнезема и железистых соединений. В отличие от зол и шлаков горелые породы почти не содержат стекловидных компонентов и характеризуются высокой сорбционной способностью. Содержание несгоревшего топлива в глиежах достигает 2—3%, в отвальных горелых породах оно может быть более значительным.
К горелым породам, наряду с природным сырьем, относятся и перегоревшие пустые шахтные породы, содержащие минимальное (менее 5%) количество углистых примесей и минеральную глинисто-песчаную часть, обожженную в той или иной степени. Породы смешаны с отходами угля, горючих сланцев, серой и др. Под действием кислорода воздуха уголь и сера окисляются и самовозгораются, а под влиянием высоких температур (до 1000 °С) порода подвергается естественному обжигу. Органические примеси при этом частично выгорают. Наиболее интенсивно горят породы в терриконах шахт с коксующимися или антрацитовыми углями. Степень обжига горелых пород зависит от многих причин. Неравномерное поступление влаги в горячий слой породы, неравномерное количество воздуха, соприкасающегося с поверхностью породы в терриконе, а также большое количество мелких фракций, затрудняющих доступ кислорода к очагам горения, приводит к тому, что обжиг происходит крайне неравномерно, несмотря на высокую температуру в терриконе. В результате образуется материал различной степени обжига (от спекшегося до слабообожженного) с неодинаковыми физико-механическими свойствами. Неоднородность материала в терриконе — один из его существенных недостатков. Размер частиц колеблется в пределах от 40 см до долей миллиметра. В терриконах встречаются плотные и пористые разновидности горелых пород.
Золошлаковые отходы. При сжигании твердых видов топлива в топках тепловых электростанций образуются зола в виде пылевидных остатков и кусковой шлак, а также золошлаковые смеси. Они являются продуктами высокотемпературной (1200—1700 °С) обработки минеральной части топлива.
В зависимости от температурных условий образование золы и топливных шлаков возможно без плавления, в присутствии расплава и при полном расплавлении исходных компонентов. В первом случае золы и шлаки образуются при сжигании низкокалорийных видов твердого топлива. Получение из расплава характерно для гранулированных топливных шлаков. Наиболее характерно получение топливных зол и шлаков в результате взаимодействия расплава с твердыми фазами.
Образование шлаков и зол первых двух групп происходит обычно в слабоокислительной среде, что способствует окислению органических соединений и сульфидов и присутствию соединений железа в трехвалентном виде. Образование отходов третьей группы происходит в восстановительной среде, что приводит к сохранению сульфидной серы и преобладанию двухвалентных соединений железа.
Зольная часть Донецкого, Печорского, Кузнецкого, Карагандинского и ряда других бассейнов содержит не более 8-10% СаО. Высококальциевой зольной частью с содержанием СаО 15-40% характеризуются каменные и бурые угли ряда бассейнов Средней Азии и Сибири, многие типы торфа и горючие сланцы. У последних содержание в зольной части СаО составляет 25-60%.
Топливо сжигают в слое над колосниковой решеткой в виде мелких кусков или при вдувании в пылевидном состоянии. Золы-уноса пылевидного сжигания проходят высокотемпературную обработку. Они имеют сравнительно однородный химический состав и незначительное содержание несгоревших частиц топлива. Некоторая часть золы оседает на трубах котла, поде и стенках топки, но основная ее масса (зола-унос) уносится с дымовыми газами, улавливается и скапливается в бункерах, откуда удаляется потоком воды или пневмотранспортом. На большинстве действующих ТЭС применяют систему гидроудаления для транспортирования золошлаковых смесей в отвалы.
Зола-унос представляет собой тонкодисперсный материал, состоящий в основном из частиц размером 5-100 мкм. Ее химико-минералогический состав соответствует составу минеральной части сжигаемого топлива. Например, при сгорании каменного угля зола представляет собой обожженное глинистое вещество с включением дисперсных частиц кварцевого песка, при сгорании сланцев — мергели с примесями гипса и песка. При обжиге минеральной части топлива дегидратируется глинистое вещество и образуются низкоосновные алюминаты и силикаты кальция.
Зола-уноса
Таблица — Химический состав зол-уноса электростанций Ростовской области
Содержание элементов в расчете на оксиды п.п.п.
SiO2 TiO2 Al2O3 Fe2O3 СаО MgO K2O Na2O SO3 СаОсв
Величина, % <12
43,52-61,07 0,7-1,6 18,66-24,74 9,3-13,25 2,35-4,5 1,2-2,9 3,0-4,1 0,4-1,1 <0,5 0,00
Таблица – Потребительские свойства зол-уноса электростанций Ростовской области
Насыпная плотность, кг/м³ 750 — 900 Влажность,% не более 1 Удельная поверхность, см²/г не менее 1500 Остаток на сите № 008, % по массе не более 15 Класс опасности для окружающей природной среды V (безопасные) Класс радиационной безопасности согласно ГОСТ 30108-94 и НРБ-99 I (Аэфф<370 Бк/кг) Гранулометрический состав Сито, мм 0.34 0.34-0.25 0.25-0.14 0.14 — 0.071 0.071 Фракция, % 1.76 98.24 Золы-уноса подразделяются на высококальциевые (СаО > 20%) и низкокальциевые (СаО < 20%). Для первых преобладающими являются кристаллические фазы, для вторых — стекло и аморфизованное глинистое вещество. Высококальциевые золы в свою очередь делят на низкосульфатные (SО3 < 5%), получаемые при сжигании угля и торфа, и сульфатные (SО3 > 5%) — при сжигании сланцев.
Интегральной характеристикой химического состава зол служит модуль основности МО, который для основных зол составляет МО > 0,9; кислых — 0,6-0,9; сверхкислых — М0 < 0,6. В основных золах суммарное содержание СаО + MgO достигает 50%, в сверхкислых — 12. Последние являются более распространенными.
Шлаки — основной вид отходов при кусковом сжигании топлива. При пылевидном сжигании шлаки составляют 10—25% от массы образуемой золы. Шлаки образуются в результате спекания отдельных частиц на колосниковой решетке при температуре свыше 1000 °С или при охлаждении расплавленной минеральной части топлива при температуре более 1300 °С.
Шлак стекловидный
Таблица – Химический состав шлака электростанций Ростовской области
Содержание элементов в расчете на оксиды п.п.п. SiO2 TiO2 Al2O3 Fe2O3 СаО MgO K2O Na2O SO3 СаОсв Величина, % < 5 43,67-57,07 0,55-1,60 10,56-21,25 8,76-12,41 1,5-5,13 1,7-2,21 1,21-4,54 0,60-2,56 < 0,15 0,00 Таблица – Потребительские свойства шлака электростанций Ростовской области
Насыпная плотность, кг/м³ 1600 Истинная плотность, кг/м³ 2850 Удельная поверхность, см²/г не менее 1500 Класс опасности для окружающей природной среды V (безопасные) Класс радиационной безопасности согласно ГОСТ 30108-94 и НРБ-99 I (Аэфф<370 Бк/кг) Гранулометрический состав Сито, мм 10 5 2,5 1,25 0,63 0,315 0.14 Фракция, % 8 8 19 21,5 14,5 18 11 В отличие от зол, шлаки, образуемые при более высоких температурах, практически не содержат несгоревшее топливо и характеризуются большей однородностью.
Шлак удаляют гидравлическим или сухим способом. При гидравлическом способе, имеющем пока большее распространение, золы и шлаки смешиваются.
Золошлаковая смесь – смесь золы и шлака с исходными свойствами, образующаяся при совместном удалении золы и шлака гидротранспортом на тепловых электростанциях.
Золошлаковая смесь
Таблица – Химический состав золошлаковых смесей электростанций Ростовской области
Содержание элементов в расчете на оксиды п.п.п. SiO2 TiO2 Al2O3 Fe2O3 СаО MgO K2O Na2O SO3 СаОсв Величина, % <18 48,5-53,2 1,0-1,4 23,3-26,1 11,3-13,0 2,52-3,01 2,0-2,2 3,8-4,7 0,9-1,2 <0,5 0,00 Таблица – Потребительские свойства золошлаковых смесей электростанций Ростовской области
Насыпная плотность, кг/м³ 900 — 1000 Влажность, % не более 1 Удельная поверхность, см²/г не менее 1500 Остаток на сите № 008, % по массе не более 15 Класс опасности для окружающей природной среды V (безопасные) Класс радиационной безопасности согласно ГОСТ 30108-94 и НРБ-99 I (Аэфф<370 Бк/кг) Учитывая, что многие минеральные и органические отходы по своему химическому составу и техническим свойствам близки к природному сырью, а во многих случаях имеют и ряд преимуществ (предварительная термическая обработка, повышенная дисперсность и др.), применение в производстве строительных материалов промышленных отходов является одним из основных направлений снижения материалоемкости этого массового многотоннажного производства.
Использование промышленных отходов обеспечивает производство богатым источником дешевого и часто уже подготовленного сырья; приводит к экономии капитальных вложений, предназначенных для строительства предприятий, добывающих и перерабатывающих сырье, и повышению уровня их рентабельности; высвобождению значительных площадей земельных угодий и снижению степени загрязнение окружающей среды. Повышение уровня использования промышленных отходов является важнейшей задачей государственного значения.
На основе применения отходов промышленности возможно развитие производства не только традиционных, но и новых эффективных строительных материалов. Новые материалы обладают комплексом улучшенных технических свойств и в то же время характеризуются наименьшей ресурсоемкостью, как в процессе производства, так и при применении.
5 Май 2014
Рубрика: Полезная информация